Put to the Ultimate Test – Part 4: Kink and Abrasion Tests
During the development of our cables and wires, we vigorously test each product in our testing laboratories. In the fourth part of our series, we’ll introduce you to our kink and abrasion tests.
Cables used in dynamic applications are subjected to a variety of mechanical loads, including abrasion. These occur via contact with other machine components, for example. Constant rubbing can lead to long-term damage or destruction of the sheath and core insulation of the cable. This damage can lead to cable breaks, malfunctions, short circuits, and fires.
In our testing laboratories, we therefore run abrasion tests to evaluate the suitability of our sheathing and insulation materials against the demands of everyday use. To test this, a metal pin is rubbed back and forth against a fixed cable, resulting in friction. In our testing facilities, it is possible to reach speeds of 400 mm/s and a max. acceleration of 2,000 mm/s2. Through this, we are able to accurately simulate highly dynamic applications ourselves to determine what effects friction has on the function and longevity of our products.
Bending loads are also a part of everyday life for cables and wires in many moving applications. Just as with friction, bending motions can cause irreparable damage to cable materials over time. We therefore perform special kink tests on our products to determine their resilience and to avoid unpleasant surprises.
In these tests, the cable is inserted into a moving device and is kinked at a predefined location. The testing equipment reaches angular speeds of 440°/s, accelerations of 2,000°/s2, and a maximum torsion angle of ±180°. For our engineers, a cable only passes when it is able to withstand these extreme mechanical loads without sustaining damage.
Ask the Expert
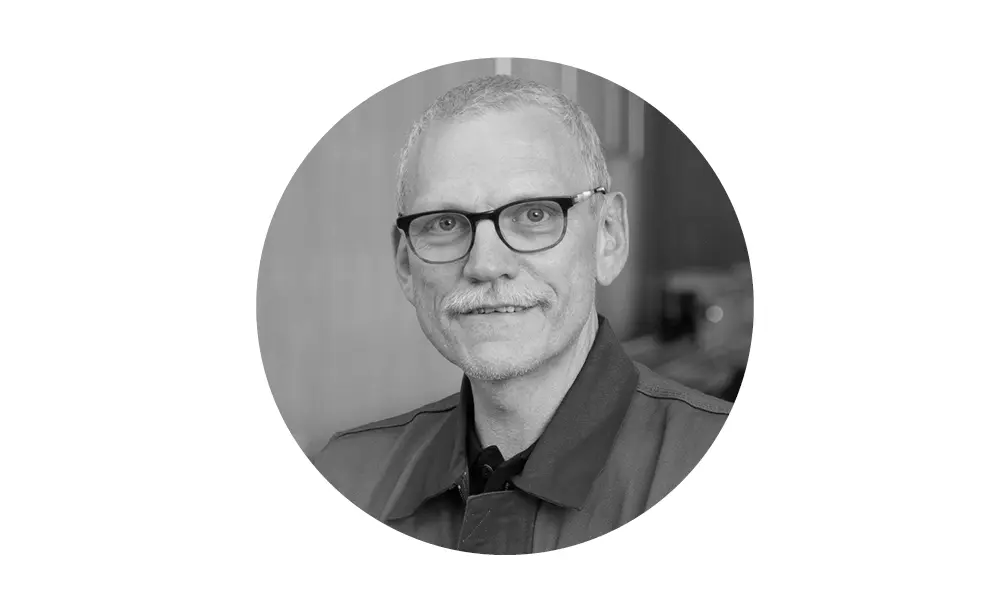
Günter Meyer is Head of Dynamic Testing at the HELUKABEL plant in Windsbach
How can I best protect cables and wires against abrasion?
There are a number of ways. The best way would, of course, be to avoid potential contact points between cables and other components in the designing phase of moving applications. This, however, is not always possible. If I know that friction may occur, then the choice of appropriate sheath material is important. Cables made of polyurethane (PUR) have the highest resistance to friction. Even other thermoplastic elastomers (TPE) exhibit a high abrasion resistance. Polyvinylchloride (PVC) is, however, is not as resistant. It is also possible to protect cables from abrasion using additional sheathing, such as using heat-shrink tubing, braided sleeving, or fabric tape. In some circumstances, the incorporation of a cable trough or a drag chain can help protect the cable and avoid abrasion.
What exactly is cable breakage and why is it so dangerous?
A cable break occurs when the cores of a cable partially or fully break apart due to mechanical overload such as abrasion or kinking. The electrical connection is completely disrupted at this location. This can also mean that the electricity that normally flows through the now broken part is instead flowing through the remaining portions of the cable, which can lead to increased current densities. The cable will begin to heat up, damaging the core insulation and the sheath. This could result in short circuits or electric arcing, which themselves could cause a cable fire, which statistically is one of the most common causes of fire. This is why it is so important to pick appropriate cables and wires for every application and to monitor these regularly.
You can also find this and many other exciting articles in the current issue #15 of our customer magazine POWER. Read it now!